Researchers at Johns Hopkins University have come up with a better prosthetic hand that uses a hybrid design to carefully grip various objects with just the right amount of pressure.
The robotic appendage combines rigid and soft components to mimic the natural structure of the human hand, as well as a range of sensors and a system to deliver feedback to the user’s nerves. In experiments, it successfully picked up and manipulated 15 different objects, including delicate stuffed toys, cardboard boxes, pineapples, metal water bottles, and even a flimsy plastic cup filled with water – without denting or damaging them.
“We want to give people with upper-limb loss the ability to safely and freely interact with their environment, to feel and hold their loved ones without concern of hurting them,” explained Sriramana Sankar, a biomedical engineering PhD student who led the research project. Sankar presented these findings in his first author paper, which appeared in Science Advances this week.
Bionic Hand Grasps Like Human
The prosthetic device closely resembles a human hand, with five articulating fingers made using soft rubber-like polymers, and a rigid 3D-printed skeleton. Three layers of bioinspired tactile sensors allow it to properly grasp and distinguish between a wide range of objects. The fingers have air-filled joints which can be controlled with the forearm’s muscles.
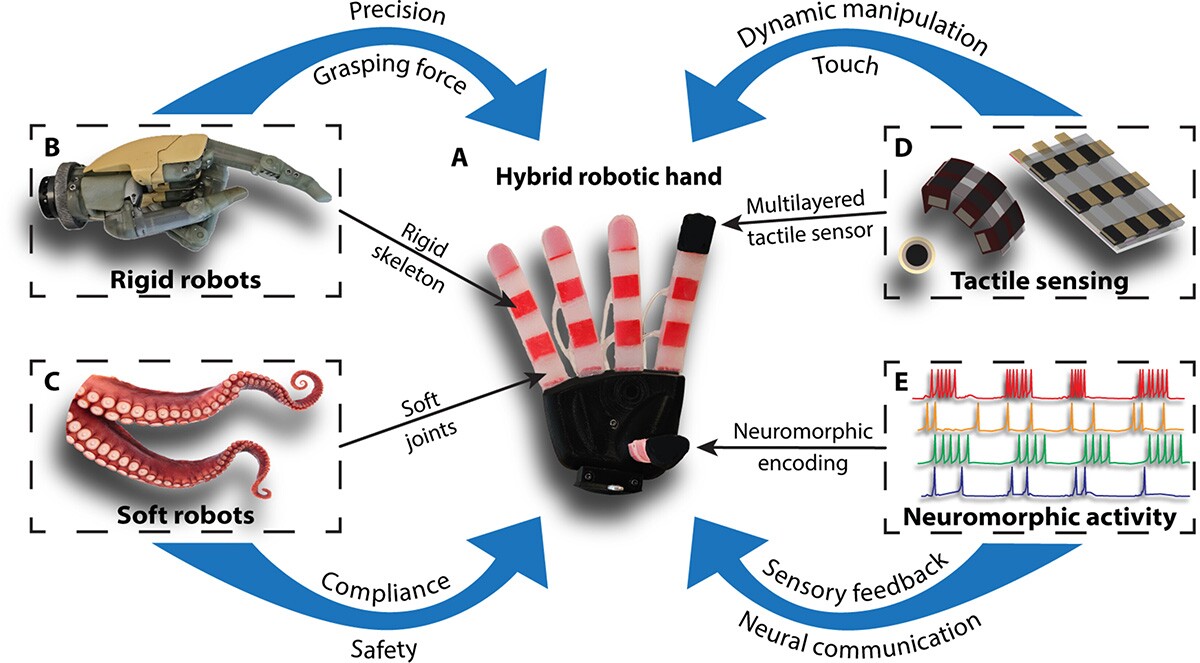
“The sensory information from its fingers is translated into the language of nerves to provide naturalistic sensory feedback through electrical nerve stimulation,” Sankar said. That’s thanks to machine learning algorithms which focus the signals from the sensors before they’re directed back to nerves in the user’s body – similar to other prostheses.
These signals bridge the brain and nerves, allowing the hand to react to what it’s touching. This system enables a more intuitively usable robotic hand that’s a fair bit more like the real thing than similar efforts we’ve seen before.
Currently, the robotic hand can be controlled using EMG signals, which are traditionally used by people with upper-limb loss to control myoelectric prosthetic hands. A US$150 gesture-control device called the Myo Armband picks up and classifies the EMG signals, and the hand positions are sent to an Arduino microcontroller for pneumatic actuation of the robotic hand.
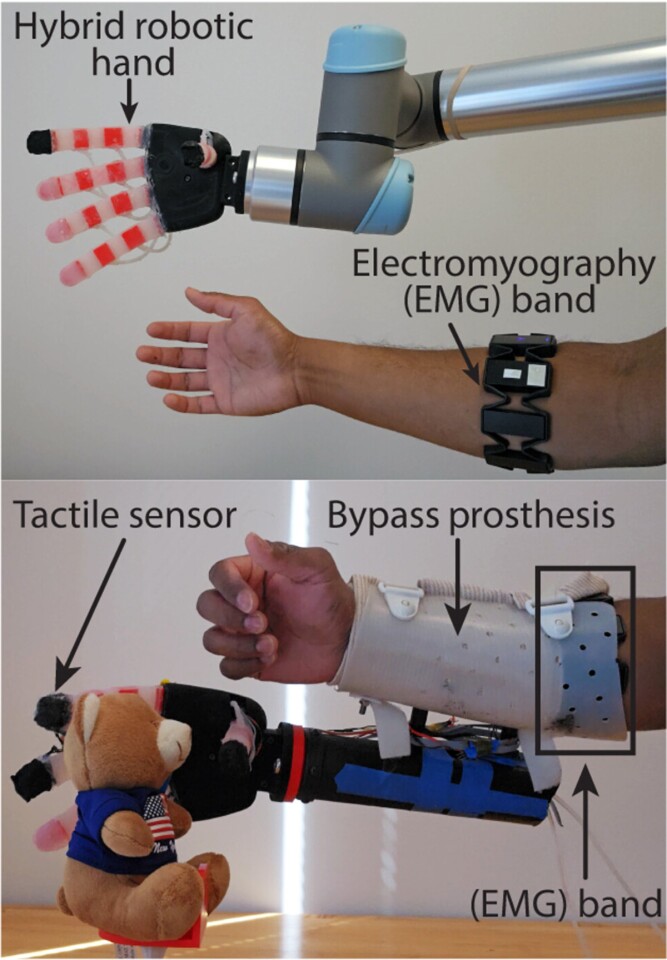
“If you’re holding a cup of coffee, how do you know you’re about to drop it?” said Nitish Thakor, who directed the research. “Your palm and fingertips send signals to your brain that the cup is slipping. Our system is neurally inspired – it models the hand’s touch receptors to produce nerve-like messages so the prosthetics’ ‘brain,’ or its computer, understands if something is hot or cold, soft or hard, or slipping from the grip.”
That goes a fair bit further than previous efforts we’ve seen in the advancement of prosthetics. Last year, scientists in Italy presented a way to detect the temperature of objects a prosthetic hand came in contact with. And way back in 2021, a joint project between MIT and Shanghai Jiao Tong University demonstrated a prosthetic hand that precisely inflates individual fingers made of a soft elastomer to grasp objects and deliver tactile feedback.
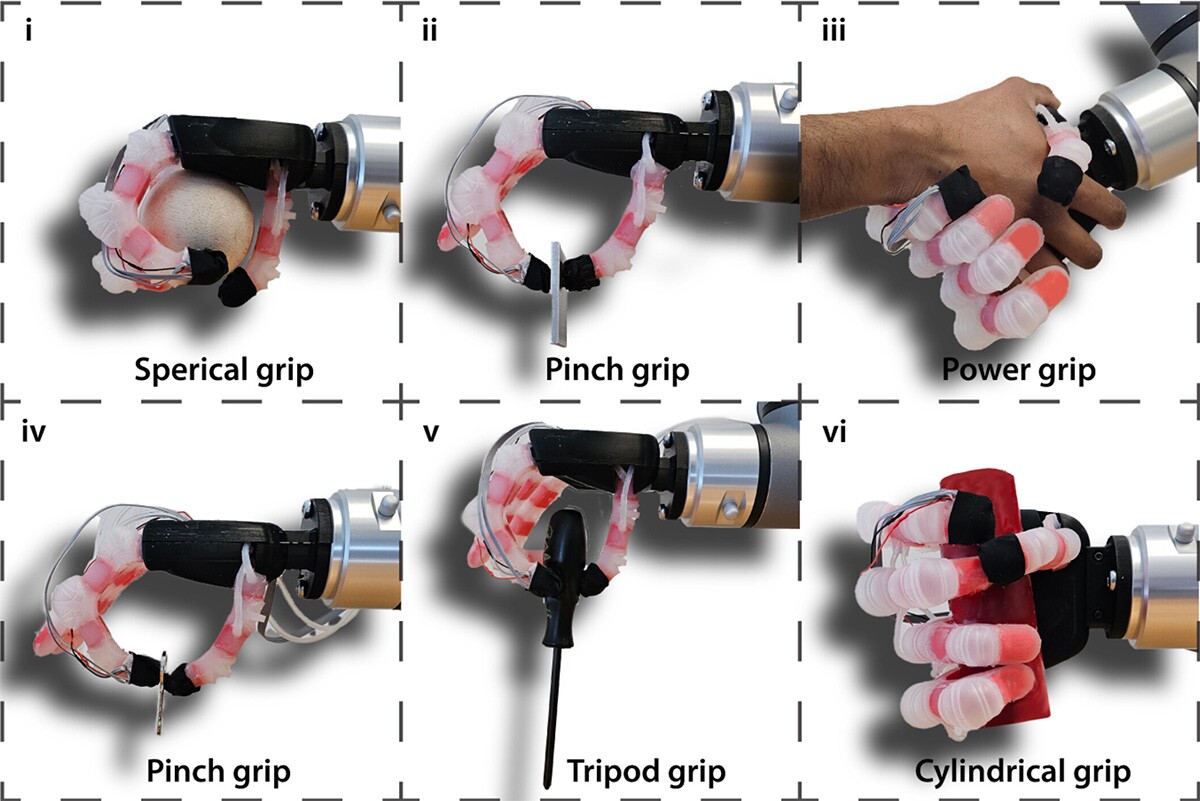
This new hand could unlock more precise, natural-feeling prostheses for amputees – and also enable greater dexterity for humanoid robots tasked with handling delicate items around your home, and on the assembly line to build more bots.
The team will continue to develop this device by exploring the addition of stronger grip forces, more sensors, and higher quality materials.
Source: Johns Hopkins University